Don’t Wait on Reciprocal Switching to Fix Freight Rail Problems
How manufacturers and railroads can short circuit a reliance on Reciprocal Switching
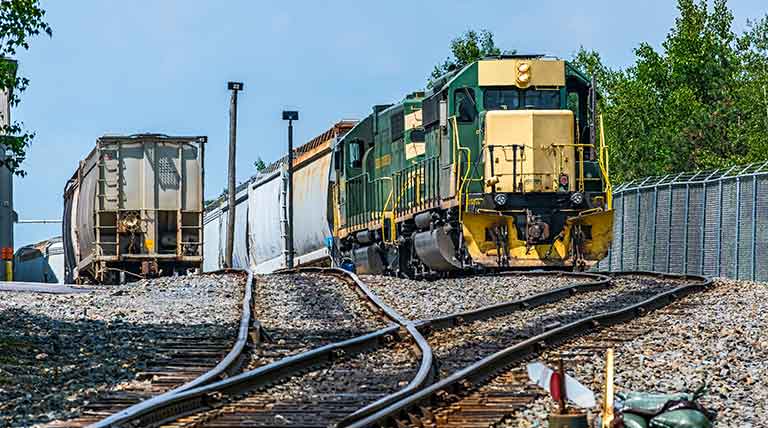
For years, railroads and rail shippers have been at odds over both perceived and real inequities in their relationships. The issue centers around the captive rail shippers that only have access to a single railroad at certain production facilities. When that railroad is late or otherwise provides inconsistent transit or switch service, the rail shipper/receiver can get bottlenecked. But it’s not always the railroad that’s to blame, a lack of knowledge on the shipper’s part can also create delays and other problems.
The issue came to a head in 2017, when a large railroad implemented a new strategy that left two major food manufacturers unable to ship their products. The railroad’s strategic changes overwhelmed the system. Both CPG companies were left without rail service that forced them to stop production. And neither had the option to use an alternative carrier due to the location of their facilities. Both manufacturers had to ship via truck to offset the rail service which dramatically increased their transportation spend.
The manufacturers filed Emergency Service Orders (ESOs) with the federal regulator that oversees railroad policy. The ESOs formally requested permission to allow the manufacturers to temporarily use another railroad. A year later, the requirements to file the ESO still weren’t met because of intensive administrative requirements. Both manufacturers threw in the towel on the ESO process.
The purpose of an ESO is to provide an “immediate alternative” to a captive rail shipper, but it clearly didn’t deliver. Since then, railroads, manufacturers, and organizations like the National Industrial Transportation League (NITL) and the Private Railcar Food and Beverage Association have been working with the federal regulator on a solution for some time.
In September of 2023, a notice of public rulemaking to allow for Reciprocal Switching was issued– acting on a request by NITL in 2011 – to provide captive rail shippers with more options.
The slow pace to resolve the issue can be attributed, at least in part, to the fact that nobody really likes the solution. Both railroads and rail shippers have found the new rules lacking. And it may take years longer before a satisfactory resolution can be reached.
So, what can be done to help ease the problem until then? From my vantage point of working with both rail shippers and railroads, there are simple solutions that if deployed on both sides could help ease a lot of the pain. In many cases, small mistakes in process execution in the switching yard and at the rail docks snowball into bottlenecks that hurt both parties.
Railroad Execution Opportunities
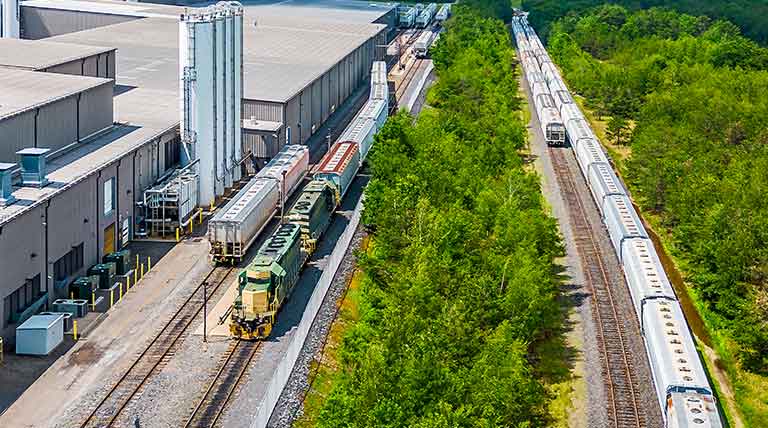
On a recent trip to visit a Class 1 railroad, I saw the most incredible training facility. The company was using VR headsets to simulate problems and they had fully functioning locomotives and boxcars – all to provide a realistic environment for employees to learn.
But when training is over and those new conductors and engineers are out in the yard, they had nothing but their own notebooks to refer back to. The sad, neurological fact is that employees only retain 20% of what they learn during training. With tools like VR and longer training periods, that number can go up, but not by much.
One Class 1 railroad recently graduated a new class of engineers and conductors. Unfortunately, when those new employees were deployed in the field, many of them felt overwhelmed by the demands of the real day-to-day requirements and they quit. This left the railroad shorthanded and without the labor needed to complete their daily deliveries of railcars.
I recently attended a meeting where a group of private railcar shippers were complaining about the continued lack of on time delivery and missed switches by the railroads. The rail shippers/receivers commented that there was no consistency in service. They either got too many railcars placed or they did not get enough. This created a tremendous burden on the rail shipper/receiver and several bottlenecks were created as a result.
The railroads should provide their employees a consistently updated, single source of truth for procedures and troubleshooting. With the ability to call up critical information on the fly, railroad crews could quickly address small issues before they became major bottlenecks or safety problems.
This could be particularly helpful at the inbound receiving facility as well. Each facility is different. Retaining a knowledge repository of best practice profiles for each facility so the conductor can quickly refer back to known nuances about the location would prevent them from having to relearn each time.
Manufacturer Execution Opportunities
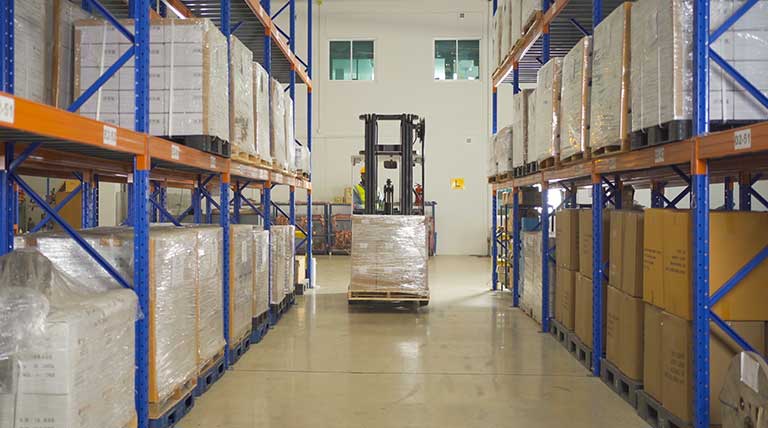
The onus shouldn’t just sit with the railroads. There is ample room for improvement on the shipping side as well.
Receiving and unloading a railcar is a unique art, leaving many receiving facilities stumped on what to do when the railcar is delivered to their dock door. Training for ordering, scheduling, and load optimization of railcars has fallen by the wayside at many manufacturers. Instead, they rely on a dwindling number of older employees with deep experience in the space. When those operators are out on leave or retire altogether, they leave a huge gap in tribal knowledge that’s difficult to fill.
Over the last several years, many companies have grown more reliant on trucking to ship products. But with driver shortages and increased costs, freight rail has come back in favor. The challenge is rail shipping and truck shipping need to be handled differently or risk major delays. I’ve seen this firsthand several times.
In one situation, I was on site in Indianapolis several years ago to observe the unloading of a railcar. Unfortunately, the team of associates were all fairly new and what should have taken 3 hours took over 9.
The same thing happened when I was on site in Phoenix a few years after that. The warehouse crew was not comfortable loading the railcar and people were being shuttled between one warehouse building and another throughout the day to help with the loading of the railcar. That took 12 hours when it should have taken four hours maximum.
The precise loading of a railcar isn’t an arbitrary requirement. If a railcar isn’t loaded according to the American Association of Railroads (AAR) guidelines, there can be significant penalties to the rail shipper for failure to abide by the rules. Railcars must be loaded properly to avoid shifting which can inadvertently lead to a derailment.
Ideally, rail shippers would begin to train their shipping associates to specifically deal with loading and shipping railcars. But at a minimum, they need a consistently updated reference to help them identify what to do in different scenarios and remind them how to properly load the cars.
Don’t Wait for Reciprocal Switching
There’s little value in either the railroads or the rail shippers to continue to wait for this rule to be imposed. Even when it is finalized, it’s unlikely to completely solve the problem satisfactorily for everyone involved and will take another couple of years to fully implement the new ruling if imposed.
Instead, with some small investments of time and resources, both sides could improve operations to help prevent these issues from happening in the first place.
Call me. I can show you how easy it can be to get your teams better prepared to react to any situation that arises on the rails or in the warehouse.
Ready to crush your goals?
"*" indicates required fields