3 Manufacturing Trends you can’t afford to ignore
How you deploy standard work will determine your success in managing them
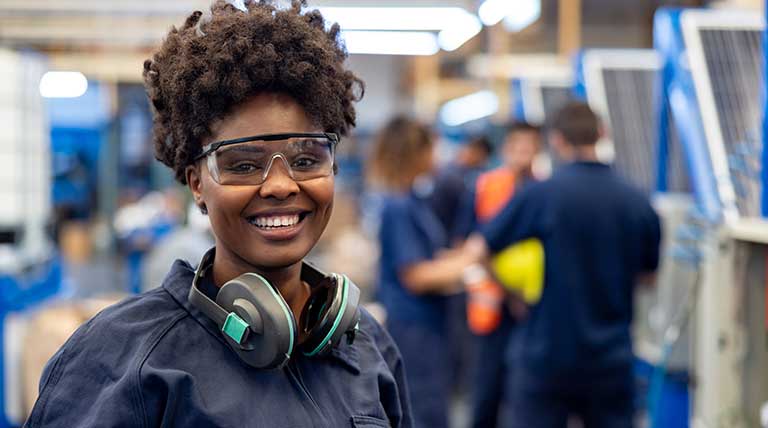
Standard work is the no brainer path to a more agile and efficient manufacturing team. You can tell, because so many variations have been invented to help refine and deploy the methodology. But the truth is it doesn’t really matter if you use Lean Six Sigma, Toyota Production System, Integrated Work Systems, or some other manufacturing operating system.
What matters is whether or not you can get your people to follow it.
Over the last several years manufacturing has experienced a wide range of challenges and increasing opportunities to improve. Here are the top three trends to focus on in 2025 and how you can master them all if you’re successful at deploying standard work.
1. Workforce Shortages & Employee Retention
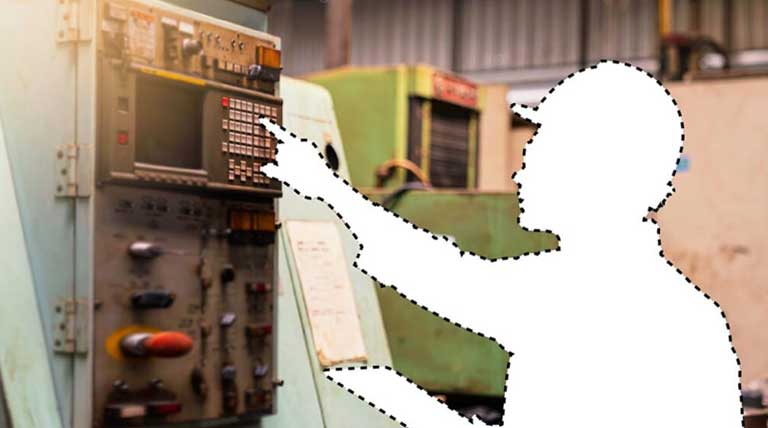
The workforce shortage plaguing manufacturing won’t let up any time soon. In fact, the US alone could require as many as 3.8 million new employees by 2033. Of those, nearly 2 million jobs will go unfilled.1
That makes employee retention a critical goal for all manufacturers. Retention continues to be a challenge for many companies, particularly among roles requiring specialized skills and experience.
High engagement leads to higher productivity, less turnover, and a better-performing company. But in 2024, only 45% of workers rated their morale as high – a decline since 2023.2
Companies that struggle:
In the simplest of terms, employee engagement drives employee retention at most companies. Those that struggle with retention are also frequently challenged to help employees feel confident in their work. Inadequate training and a lack of on-the-job resources make it difficult for employees to do the right thing. That can lead to performance anxiety and errors that create turnover.
Companies that thrive:
Engagement and overall worker satisfaction isn’t just about higher pay. Companies with high retention rates provide guidance for employees to complete standard work safely, accurately, and efficiently. That helps employees develop confidence by making training for competence an integral part of the job.
Businesses with the best retention are quick to remove unnecessary obstacles and request employee feedback to drive process improvement.
Probably most importantly, they create visibility for employee skill development opportunities and career advancement. Both incentivize employees and make the company more agile.
In other words, make it easy to do the right thing and hard to do the wrong thing.
2. Automation, Digitalization & Other Technological Advancements
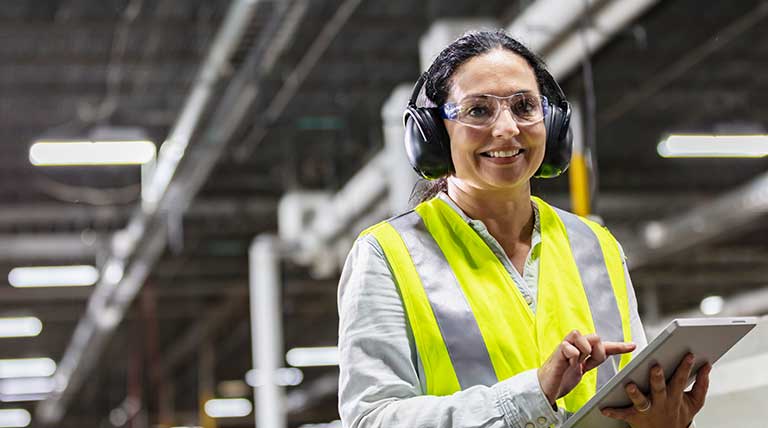
A constrained labor market makes the need for technological advancement even more relevant and urgent. But that’s not the only driver for companies investing in Industry 4.0 technologies like cloud computing, IoT, and advanced automation.3
Manufacturers that successfully incorporate technological improvements will quickly increase efficiencies, deliver on sustainability initiatives, and bring new products to market faster with fewer quality issues.
Companies that struggle:
As companies deploy new software and equipment, their ability to reap the benefits often boils down to the ability of their workforce to adapt to the new tools. Companies that struggle to manage change will struggle to show return on investments. In some cases they’ll fail to launch altogether and chalk up a major loss on investment.
Companies that thrive:
Manufacturers with a strong operating management system and a culture built around standard work are ahead of the curve. It’s easier to change processes and reskill employees if they’re already accustomed to following One Best Way processes to complete critical tasks.
Those deploying digital work instructions and other on-the-job tools can train employees on new equipment and software as they work, avoiding long periods of downtime. They’ll experience less confusion and turnover as employees view structured upskilling or cross-training opportunities as beneficial to their career.
3. Resilience & Risk Management
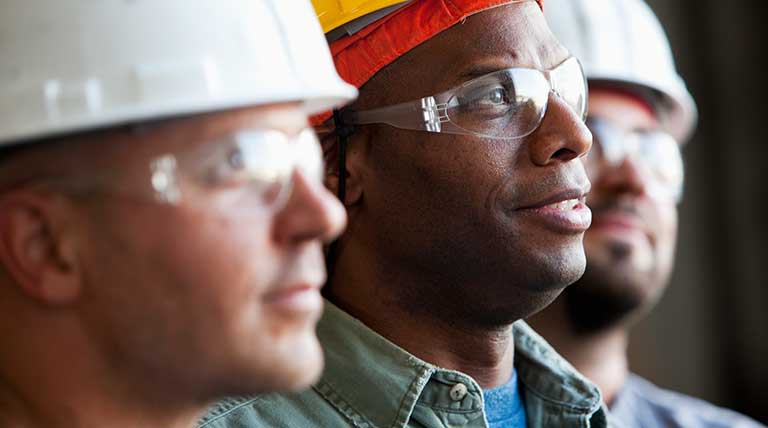
Disruption is the new normal this decade. Few anticipated the continued instability wrought by the pandemic, the global supply chain disruption, and the increasingly severe weather events we’ve been experiencing. Manufacturers that have become more agile have responded quickly to disruption.
If you feel like we’re through the worst of it, you’re in the minority. Increasingly demanding regulatory requirements,4 cyber attacks,5 and demand for supply chain resiliency6 are just a few of the likely issues we’ll face moving into the future.
While it’s important to have business continuity events prepared for any potential outcome, it’s more important that your team knows how to react when the time comes.
Companies that struggle:
Organizations that haven’t deployed standard work can’t respond quickly to the unexpected. They can’t get their employees on the same page or determine if they’re doing the right thing.
Even companies that have spent millions with consulting firms to develop intricate policies and procedures can find themselves struggling during an emergency. If protocols sit on shared drives and in binders, but never make it into employees’ hands, they’re not worth the paper they’re printed on.
Companies that thrive:
When organizations make their procedures easy to access and follow, their teams can move as one in response to a situation.
Employees who are already accustomed to accessing standard work from a dynamic, centralized system will know where to turn when they encounter the unexpected. The really good systems will enable you to instantly deploy changes that are immediately incorporated into daily activities with minimal need for prolonged training programs.
Ensure your team thrives into the future
Your success depends on your ability to develop new products to meet consumer demand for variety and quality while simultaneously delivering on shareholder demands for growth and efficiency. Increasingly, your ability to balance these objectives while dealing with unexpected curve balls is the norm.
Incorporating a platform that enables employees to autonomously follow standard work requirements is the future of how work gets done.
Whether you’re just getting started defining the standard or trying to figure out how to get your team to follow it – we can help! Reach out today, we’ll work with you to plan, prioritize, and deploy.
Sources:
- US Manufacturing Could Need as Many as 3.8 Million New Employees by 2033, According to Deloitte and The Manufacturing Institute
- “Future of Work in Manufacturing” 2024 Report
- The Future of Factories: Different Trends
- New Sustainable Manufacturing Regulations: What Manufacturers Should Know
- Manufacturing Is #1 in Cyber Attacks for Third Straight Year. What Can Be Done?
- Reshoring and Nearshoring Trends and How Advances in the Automation Industry Make North America Competitive
Ready to crush your goals?
"*" indicates required fields