76% improvement in Maintenance Technician time to proficiency
Labor shortages and improved materials handling technologies are driving rapid adoption of automation solutions among distribution organizations. In fact, 70% of top logistics and supply chain executives plan to invest in automation over the next 5 years.1
As robotics and other new equipment play a larger role in day-to-day operations, improvement in Maintenance Technician capabilities will become even more critical to keeping systems running smoothly.
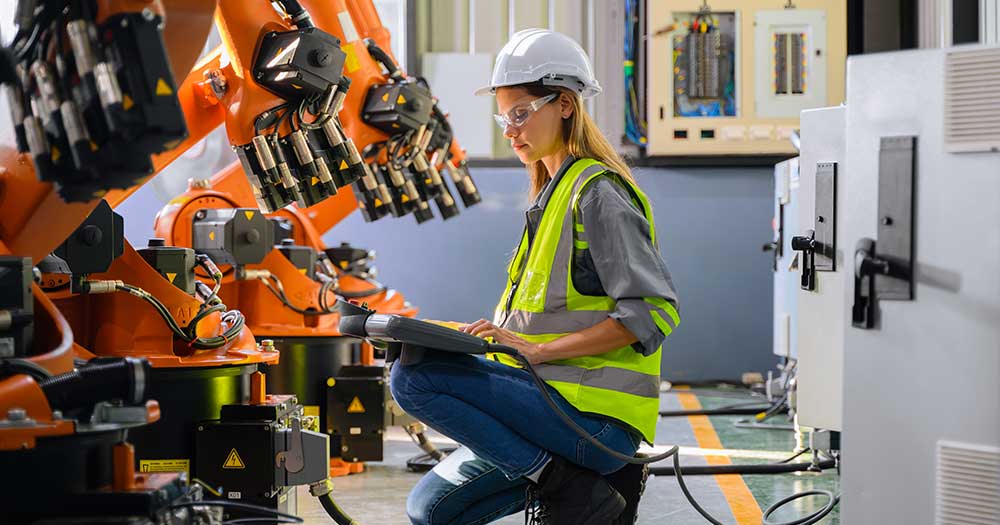
Outcomes:
- 76% improvement in maintenance technician time to proficiency
- 32% improvement in unplanned downtime of critical equipment
- 20% reduction in management time spent onboarding new hires
- Safety incident reduction due to more easily deployed safety content and one-point lessons
“We set an ambitious goal to improve uptime, and Acadia helped us close skills gaps within months.”
– Director of Maintenance Excellence
How Acadia Enabled Rapid Improvement in Maintenance Technician Proficiency
Our client is a leading manufacturer and distributor of medical supplies in the US. Their critical, lifesaving products must be delivered on time to hospitals and other healthcare providers from their 40+ Distribution Centers (DCs).
That means, the people who run and maintain their facilities, must complete their work accurately and efficiently. For example, in their most automated DCs, maintenance teams have a window of 2-3 hours every day to service the robotic order fulfillment equipment and ensure it remains operational for the remaining 20+ hours per day.
Higher reliance on maintenance and the cost of unplanned downtime meant the company needed to focus on improving training and retention for these critical roles.
Previously, it took 90 days for a new maintenance technician to become proficient in their position. Employees were led through training by supervisors which the company manually tracked in spreadsheets.
Now, technicians are assigned skills in Acadia allowing them to be a key owner of their own onboarding. As they make progress learning, progress is tracked automatically, eliminating the need for spreadsheets. After just five months, time to proficiency has improved by 76% to 21 days!
The company has also transitioned its safety training and compliance into Acadia to ensure proper execution of critical processes like Lockout Tagout, as well as tracking OSHA standards compliance.
Our client is currently transferring its Zero-Defect Maintenance Excellence program from a traditional knowledge management system into Acadia. This next step will make it easier for technicians to access all the information they need to perform critical tasks. It will ensure compliance with standard work and enable the company to deploy process improvements rapidly across the enterprise. The transition has already yielded improvements in uptime for critical labeling equipment.
Access to critical information and the autonomy to learn and work independently has led to a more engaged workforce that continues to outperform its objectives.
Sources:
Ready to crush your goals?
"*" indicates required fields