Manufacturing
Connected workers are engaged, driving continuous improvements in process and quality.
Productivity That Drives Profitability
We help you meet the challenging goals that drive profitability by improving the performance of individual team members.
Acadia digital work instructions engage employees, quickly building competence and autonomy.
We also help you connect the dots between team productivity and your operational metrics.
Improved performance from the factory floor to the back office
One Best Way work procedures are easier to follow when digital SOPs include videos and other job aids. This helps ensure everyone knows how to complete their work safely and accurately. With each individual following the same repeatable and auditable process, the ability to measure, analyze, improve and control becomes more achievable. Employees will also have room in their working memory to identify new and better ways to do things – making continuous improvement a natural part of your business with manufacturing process improvements.
See how one of our clients exceeded gross line yield goals in 6 months.
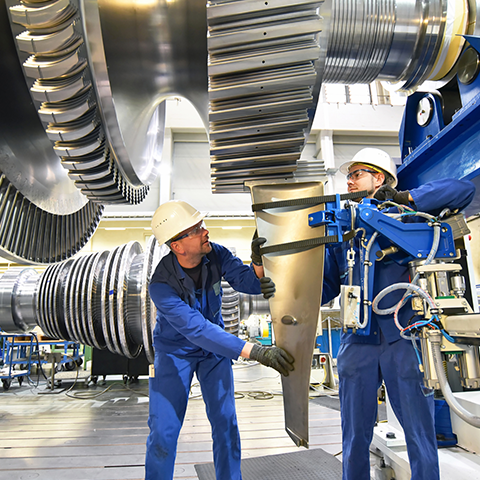
Build, track, and mobilize team skills with tools built to help you close skills gaps across your business.
Acadia helps employees understand what skills they’ve mastered and identifies a path for skills they still need to attain. This engages employees by encouraging them to take control of their own career advancement and organically improves retention.
Managers gain visibility into employee capabilities to aid in demand planning and scheduling. They can also identify employees who can fill gaps with a bit more on the job training and learning.
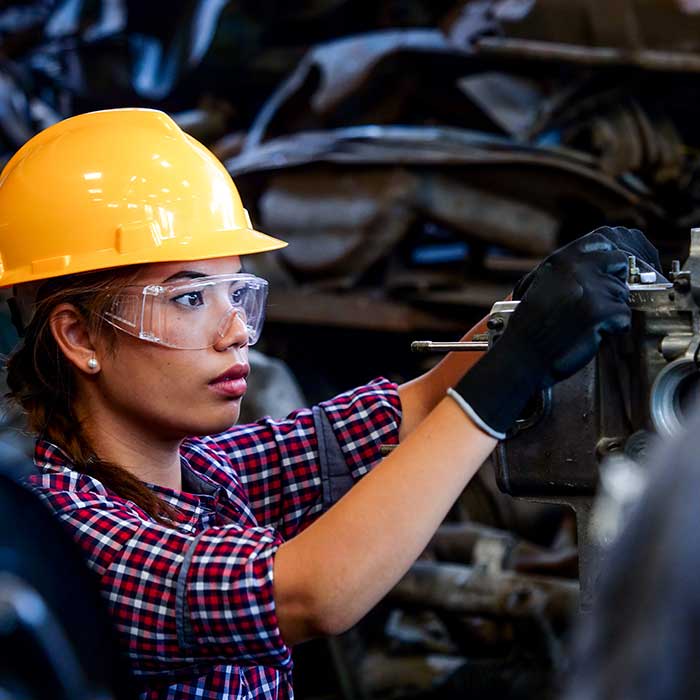
In most operations, standard work compliance correlates directly to performance. When compliance expectations are met, line yield, waste management, and safety KPIs are also improved.
Managers with visibility into employee SOP compliance can identify who is performing tasks according to One Best Way processes and who might need additional training or support. By digitally tracking compliance of policies and procedures, you also create an audit trail that can help you comply with ISO standards, OSHA regulations, or FDA guidelines.
Read how our client hit an 100% quality score audit for the first time.
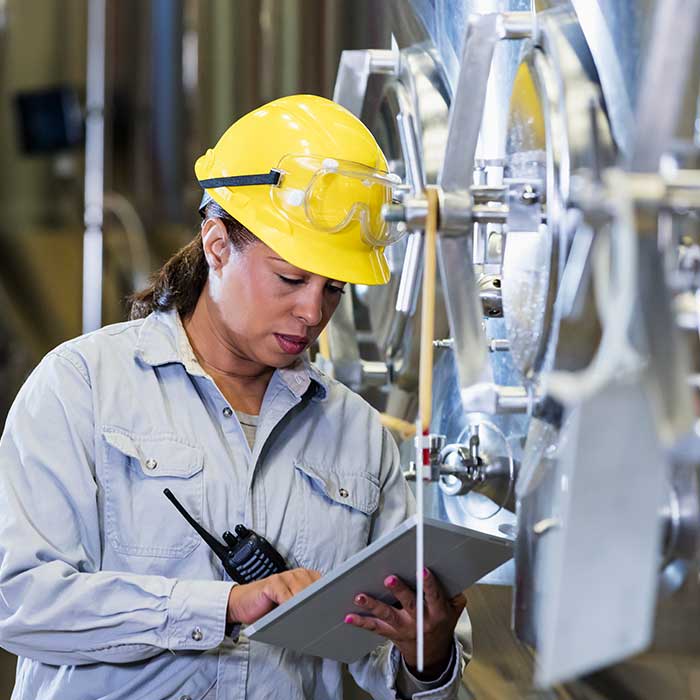
Consistent outcomes in your manufacturing process start with your training approach. We learn better while doing. Job-embedded training programs are immediately more relevant than classroom or course-based activities. They take less time. They require less effort to pay attention.
Acadia improves training effectiveness by injecting training directly into work. Employees have easy access to the right content at the moment they are performing the task. Managers can check comprehension with quizzing and evaluations to ensure everyone gets the support they need.
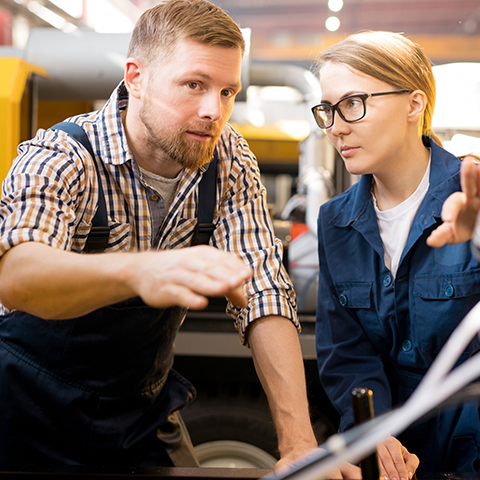
There simply aren’t enough skilled workers to meet the demand for open manufacturing jobs. Unfortunately, training in many companies isn’t effective enough to upskill or reskill existing workers to close the gaps. Skills that are learned while actively performing tasks are learned more quickly and are recalled more readily in the future.
Providing checklist guided procedures with incorporated job aids helps employees learn new job requirements quickly. Quizzing and evaluations help managers see where more training is required and who is ready for more responsibility.
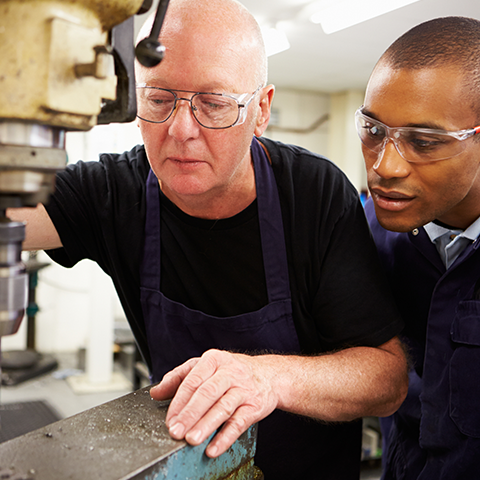
If key positions at your company are retiring in record numbers, you’re not alone. Unfortunately, this creates a huge gap in core skills and knowledge. To capture tacit knowledge before it exits the business, you need an organized system.
Acadia provides a way to not just capture information but make it easy to find and convert into training content for those replacing your retirees.
Learn how you can capture knowledge before it’s gone for good.
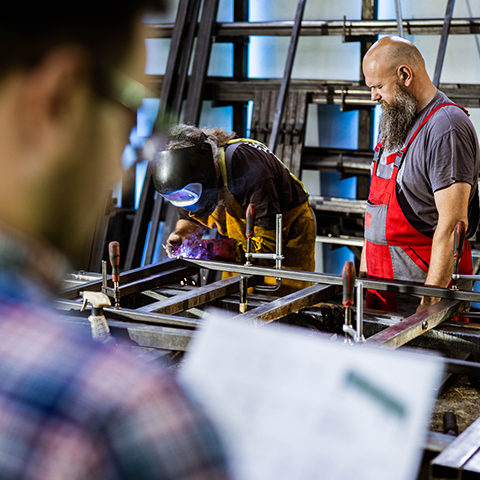
Engaged employees are more likely to remain with the organization. One of the best ways to encourage engagement is to enable your team members to contribute their ideas for how to improve their work processes. This approach is only viable, however, if managers act on the recommendations.
In Acadia, employees can provide feedback on content, processes, and other aspects of their work. The data is captured and organized so that managers can quickly identify new ideas and implement the ones that will have a positive impact. Continuous improvement thrives in an environment that encourages everyone to be engaged and contribute.
Learn the best way to capture feedback from your front line teams.
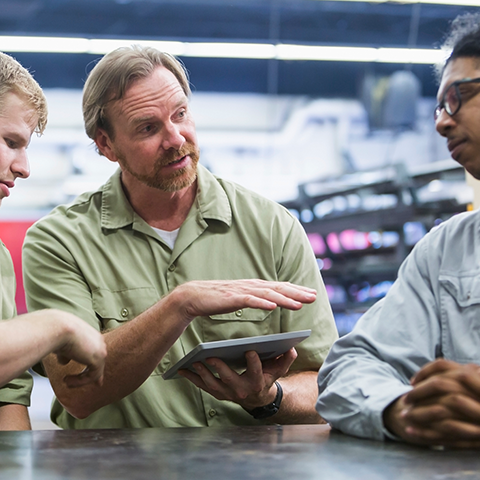
Enterprises that grow through acquisition often increase the complexity of their operations as well. Over time, redundant systems, unnecessary rework, and loss of quality can inflate the cost of acquisitions. Making One Best Way processes clear, and sharing them among all employees, helps to quickly get everyone on the same page. Acadia helps to organize all processes and procedures so that you can identify the best of the shared knowledge from each entity.
See how integrations can happen faster when you upgrade your tools.
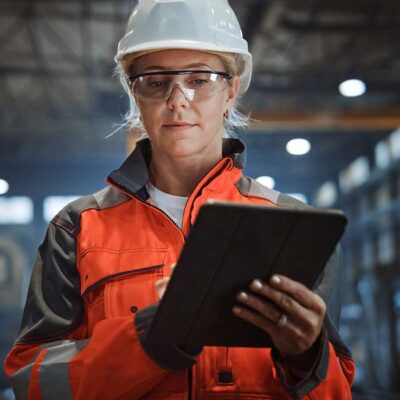
Digital Work Instructions are just one way Acadia improves manufacturing efficiency
This video shows how a line change happening across shifts could be made more efficient. Reach out to see additional ways Acadia can help make your frontline teams more proficient.
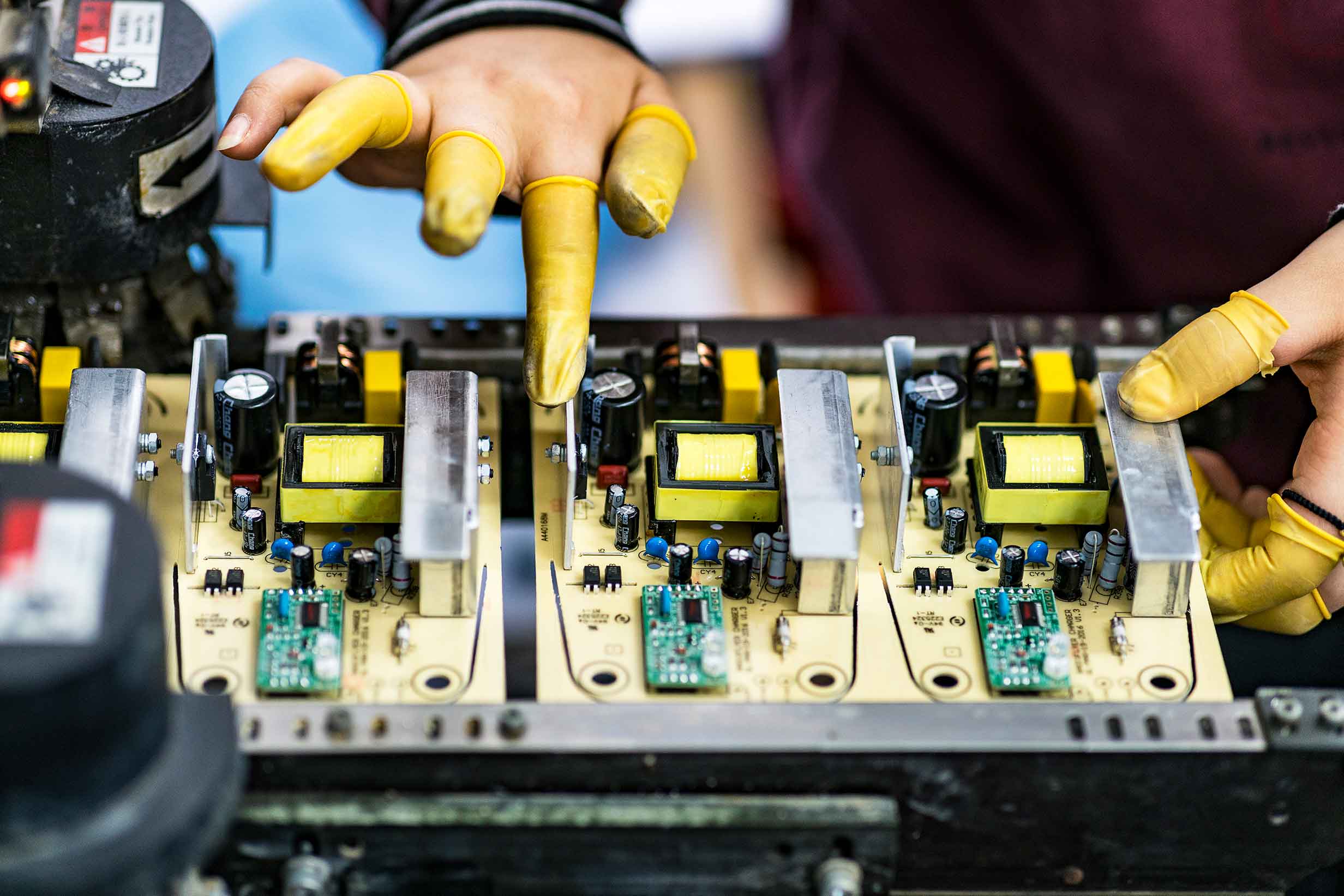
See it for yourself
Let us know if you’d like to see Acadia. We’ll show it to you with your own work instructions.
"*" indicates required fields
Autonomous Teams Built on Knowledge and Accountability
When you’re the world’s leading beer producer it’s important to maintain quality and consistency across every geography. That’s why AB-InBev has been using Acadia to build autonomous teams since 2016.
Acadia provides critical knowledge to operators running manufacturing lines across the globe. Connected workers learn new skills on the job with just in time work instructions that train and guide them, ensuring One Best Way execution and team member autonomy.
Watch this short video with the Global Product Owner of Acadia at AB In-Bev.
More Real World Results
ROI Calculator
Enter your data into the model on the left-hand side of the page to see your potential savings with Acadia on the right. Calculations are based on typical Acadia client results. Click on the ▼ and ⓘ icons for additional information.
Enter Your Details
With Acadia
Calculated Current State
Acadia helps improve the overall performance of your employees. Depending on your industry, you can expect to get additional savings from Acadia in the form of waste reduction, customer retention, and other metrics associated with employee error.
Connected teams improve metrics
Acadia digital work instructions engage employees, quickly building competence and autonomy.
In a few weeks, you’ll:
- Make it easy for your team to execute critical tasks accurately
- Track your team’s compliance to understand performance strengths and gaps
- Improve processes and instantly change behavior on the front line
We’ll also help you connect the dots between team productivity and your operational metrics.
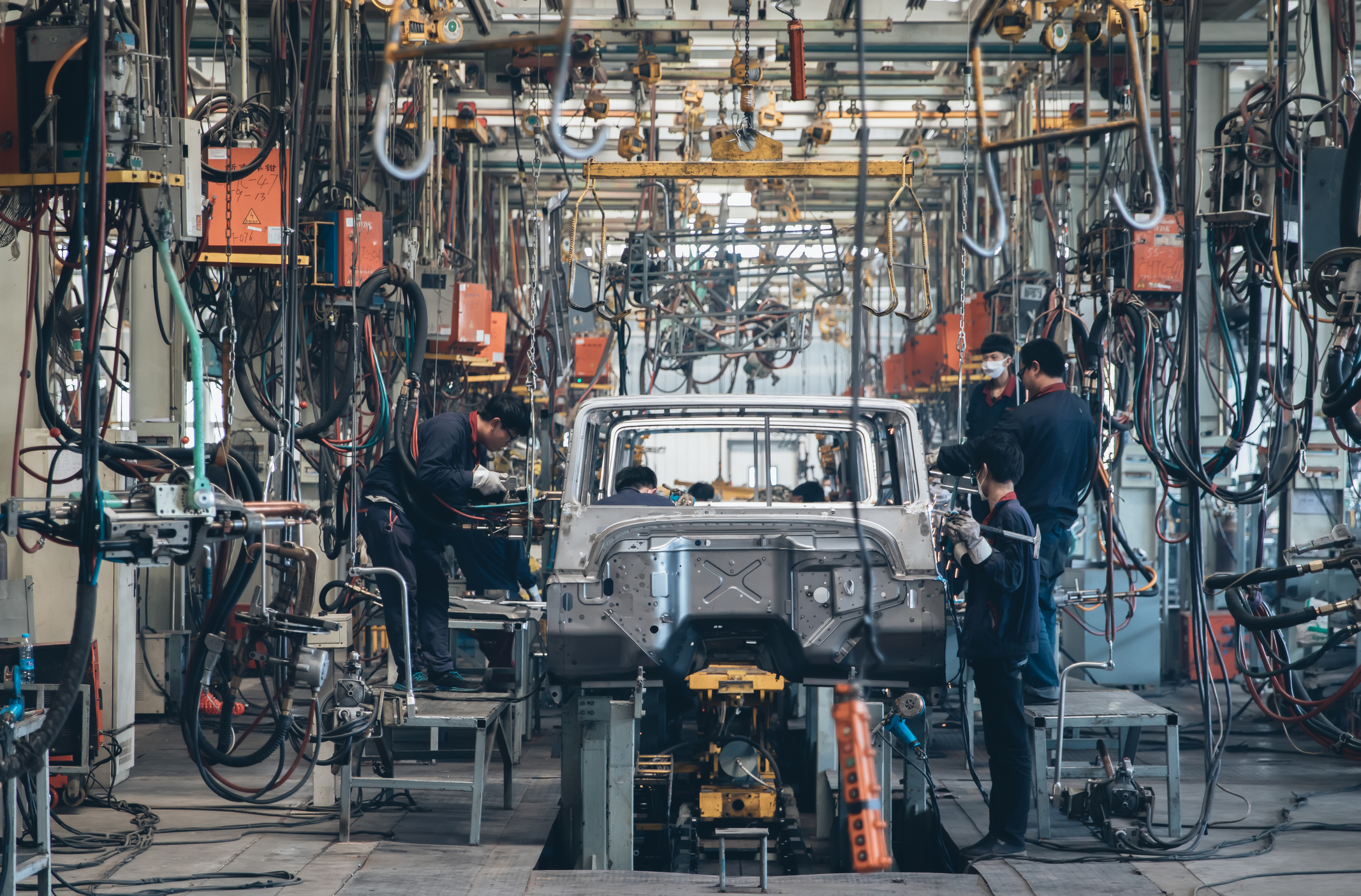
Consistency, Efficiency & Safety
Acadia provides a single source of truth that is available to employees from onboarding and training to the execution of daily tasks. One Best Way processes that are embedded from day one become second nature to employees. When changes are inevitably made, or employees uncover better ways to perform their work, you can quickly make and share updates instantly across your workforce.
The result is a reduction in production downtime and workplace accidents, and an improvement in product quality and employee retention.
Why Acadia
Additional food for thought
See Acadia in action, ask for a demo
"*" indicates required fields