Prepare for the Next Disruption
Connected Workers are better trained, more agile, and enabling rapid transformational change
- Connected Workers are the key to agility in today’s disruptive environment.
- Continuous improvement of both processes and employee capabilities are key to building agile teams who can adapt on demand to the unexpected.
- Learning while doing increases knowledge retention that classroom and LMS-based training alone can’t.
- The right Connected Worker platform bridges the gap between current operations and a more agile future.
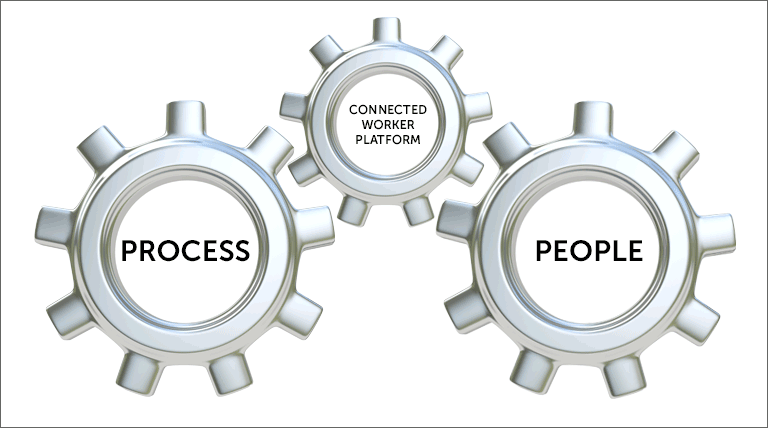
If you’re over the age of 30, you probably owned or at least remember several of the devices on this RadioShack ad from 1991. Now, you can do all this and more with just your phone.
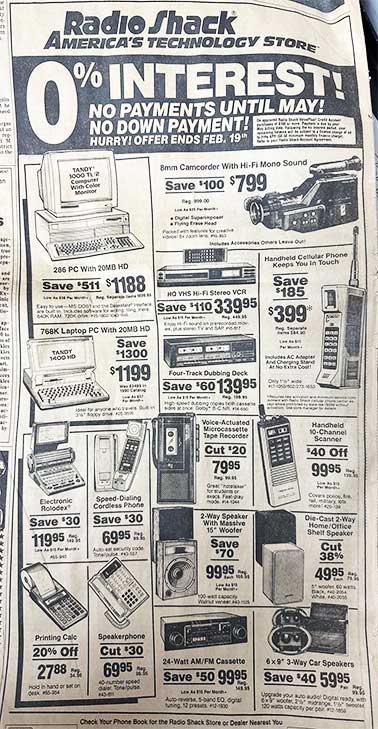
Technological advancements like these have dramatically influenced our personal lives. But many of us have felt the effect even more profoundly in our day-to-day work.
While our businesses have adopted sophisticated software platforms and robotics to automate processes, people have largely been ignored in the equation. In fact, most people are being trained to use new technologies with tools that hit their peak when that RadioShack ad first ran in the newspaper.
There are 5 realities impacting your business right now:
- External disruption is the new normal
- Employee role requirements are increasingly complex
- Traditional training methods are ineffective
- Employee retention is critical and harder than ever
- Incremental continuous improvement is mandatory
While nearly every business is attempting to navigate these challenges through transformational change, only 12% are successful.1 That’s because the way we’ve been taught to learn and work is perfectly suited for a world that no longer exists.
External Disruption is the new normal
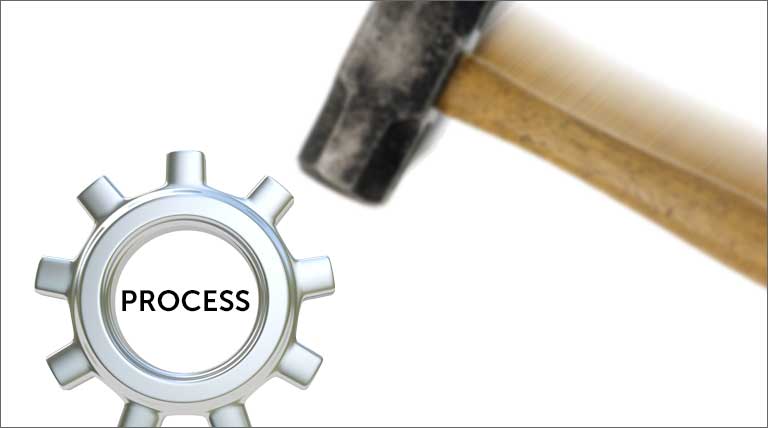
Disruptions – from natural disasters to unanticipated competitors – have been part of business planning exercises for decades. But the COVID-19 pandemic really opened our eyes. It reshuffled the global workforce, created a worldwide supply chain disruption, and set off other economic ripples we’re still feeling today.
Since then, there seems to have been an escalation in disruption. The only constant is the acceptance that we’ll need to react to something every year, even if we don’t know what it will be. Businesses are learning that an inability to shift gears based on events on the ground can quickly put you in a bad spot.
The answer for most is to develop agile processes, infrastructure, and teams that can adapt on demand. The need for rapid shifts toward agility has resulted in one in three large organizations deploying a transformation program at any given time.1
The successful ones view change as a continuous process, “integrating it into the company’s operating rhythm.” The rest will be just as unprepared for the next boat that gets stuck in the Suez Canal.
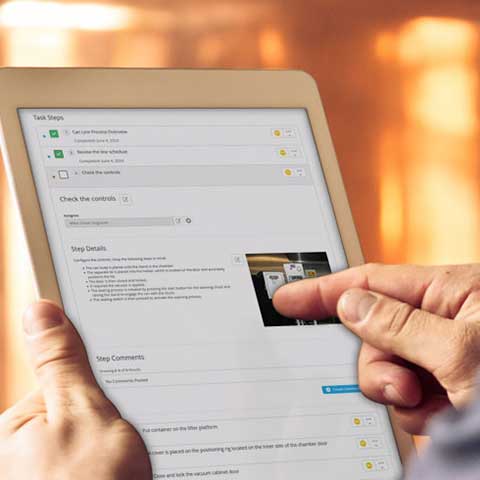
During the pandemic, one of our clients converted a production line from manufacturing beer to manufacturing hand sanitizer. Employees were accustomed to using Acadia as their single source of truth for work procedures. So, when new protocols were developed for hand sanitizer, people working that line transitioned easily to the new product. They could continue to follow instructions from the system and were essentially training on the job.
Employee role requirements are increasingly complex
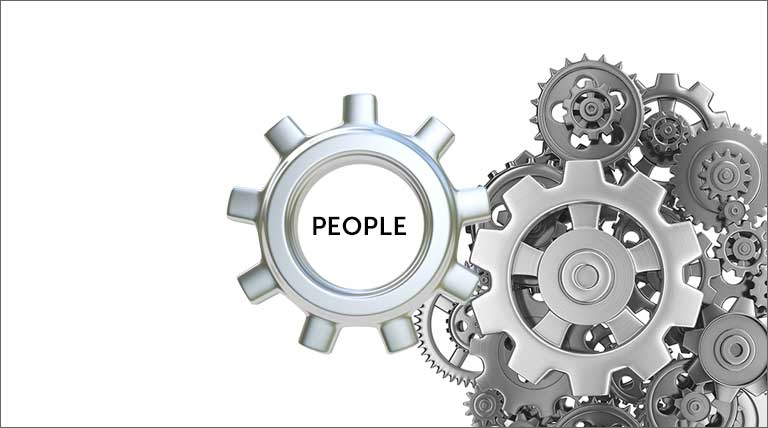
Transformation projects almost always result in radical change for employees – increasing their responsibilities and requiring more intricate knowledge to perform daily tasks. In fact, it’s predicted that nearly half (44%) of employees’ core skills will be disrupted within the next three years.2
Without a concerted reskilling effort and easy access to on-the-job knowledge tools, those that attempt to adopt new technologies often see their investments underperform or fail altogether.
People aren’t evolving at the pace of technology. We’re still limited by the hardware that determines how quickly we can learn. For those who want to deploy technology to leapfrog their competitors, the need to improve employee performance is key.
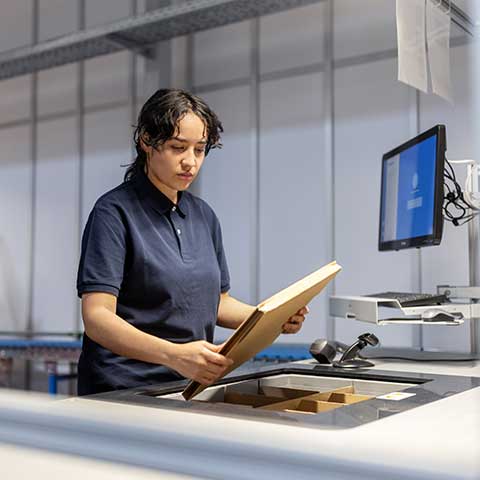
To increase efficiency in a distribution center, our client invested in autonomous mobile robots and vertical lift modules. Introducing such a transformational change in facility operations meant that everyone on the team immediately had a skills gap. In total, 600 employees were re-trained to do all or parts of their job in a few months, with virtually no downtime.
Traditional training methods are ineffective
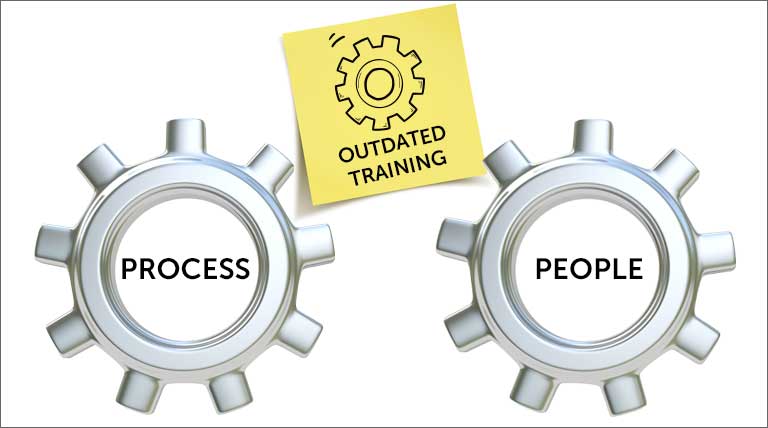
While a vast majority of companies are looking to adopt transformational technologies in the next five years,3 only half of US companies have formal training strategies in place.4
Those that do have formal training programs are deploying training that doesn’t meet the need. Classroom and LMS-based training take people out of the work environment where only 5% of training is committed to memory.5
Alternatively, on-the-job training yields 75% knowledge retention and enables employees to be productive as they learn. The combined efficiency means training can take less time and cost significantly less.
Learning while doing is a practical solution for most organizations. It also lends itself to structured career development that supports company initiatives and drives employee retention.
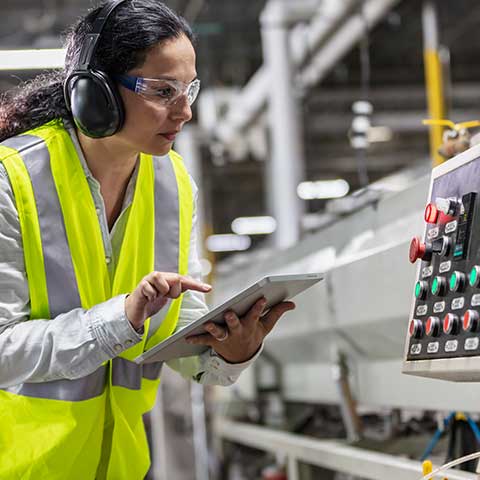
Our client transformed a paper-based training library into a dynamic knowledge repository where the entire workforce can find the information they need. Using step-by-step, on-the-job training, they reduced time to proficiency for new hires from 500+ days to 125!
Employee retention is critical and harder than ever
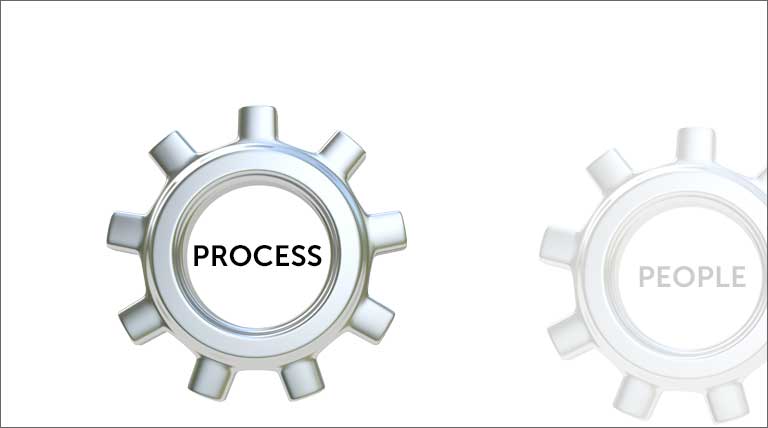
There are currently 2 million more open positions than people to fill them.6 Add to that the active exit of the baby boomers into retirement and the problem compounds.
The problem is further exacerbated by stiff competition. When employees can simply cross the street to gain a few extra dollars per wage hour, companies need to think more broadly about what they can offer.
The good news is many of the options that would help retain employees will also address some of the other challenges identified above.
7 out of 10 employees would stay with their employer throughout their career if the employer made an effort to upskill or reskill them.7 The number shifts upwards when skills training is tied to a visible career path.8
Beyond money and career opportunity, engagement and recognition9 are huge drivers of retention. These too can be operationalized. In combination with a strong continuous improvement program, you can make gains on employee efficiency alongside engagement.
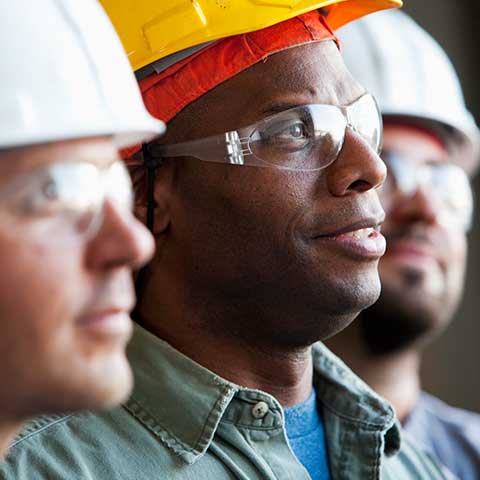
Turnover of highly skilled employees was slowing production for one of our clients that struggled to track employee skill progressions. Managers manually tracked team member training milestones and skills development in spreadsheets. Employees had no career path visibility and were quitting.
Now, both managers and employees have gained skill visibility in Acadia. Employees track their own progress alongside managers. Six months after launching Acadia in four plants, our client promoted 125 employees and radically improved retention.
Incremental continuous improvement is mandatory
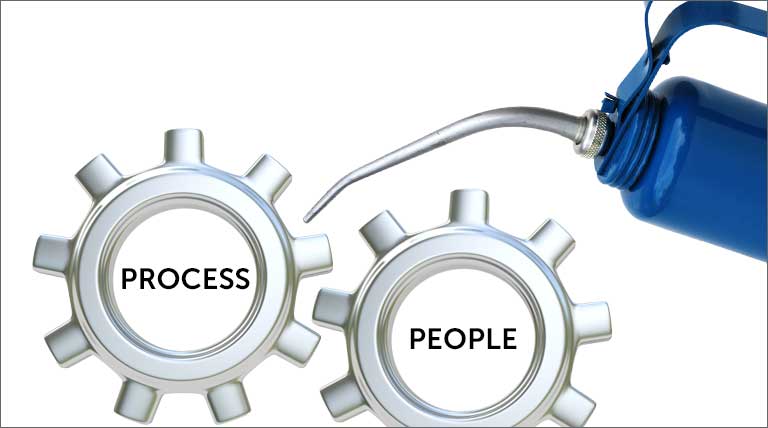
In an environment prone to disruption, companies must move quickly. That means, we won’t always nail things 100% the first time.
Investments made in continuous improvement efforts yield savings in efficiency and real dollars & cents. When implemented as part of a standard work program – the annual savings are recurring.
Additional savings and fluid innovations can be found when you actively seek out employee feedback. Employees are closest to the work and can more easily identify inefficiencies. By capturing feedback at a granular level while employees complete procedures, you’re more likely to get feedback that’s actionable.
Creating a program that recognizes employees for their ideas and follows it through to implementation helps to naturally build engagement and a sense of ownership in work.
It’s not just improvement that should be continuous. All major initiatives have the potential to fail. Taking a measured, incremental approach to deploying them can help improve your odds.
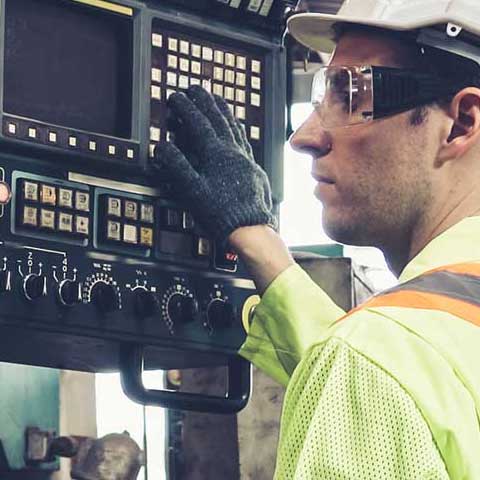
A common procedure requires planned downtime 20-30 times per day at our client’s facility. Continuous improvement managers deployed a process change using Acadia to train employees and create accountability. After just two weeks of training using the new method, the team improved downtime by 8 minutes generating $500,000 in waste and labor savings.
Connected Workers Enable Agility
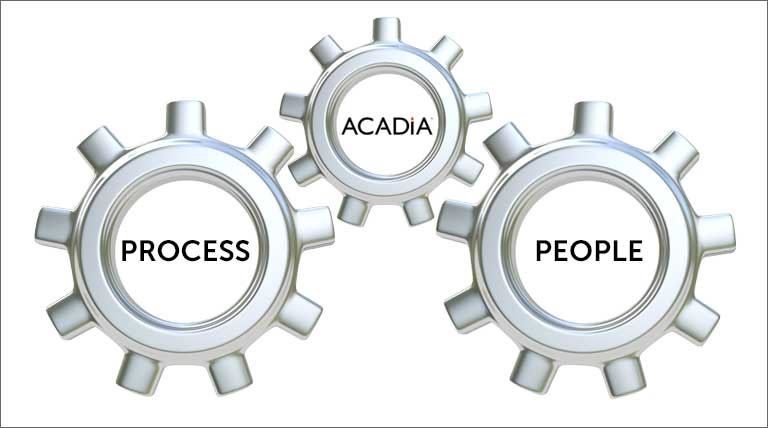
Connected Worker platforms, like Acadia, can help you bridge the gap between your current operations and a more agile future.
Connected Workers learn new skills as they work. They make fewer mistakes because they have the knowledge to make good decisions at their fingertips. They can work independently and require less hand holding by managers and peers. Most importantly, they are safer, more productive, and more engaged.
With the right Connected Worker platform, you can begin to see meaningful change, in any part of your business, in just a matter of weeks. But like any other initiative, an incremental, structured approach to adoption will yield better results in the long-term.
Call us today, we’ve been working with clients just like you to make dramatic improvements in business performance.
Sources:
- Transformations That Work
- 6 work and workplace trends to watch in 2024
- The Future of Jobs Report 2023
- 68 Training Industry Statistics: 2024 Data, Trends & Predictions
- The Learning Pyramid
- Understanding America’s Labor Shortage
- Employees Want Additional Opportunities for Career, Skills Development
- New Study Reveals Pressing Need for Transparent Growth Opportunities to Improve Employee Engagement and Retention
- Here’s the No. 1 reason why employees quit their jobs
Ready to crush your goals?
"*" indicates required fields