Fill short-term team vacancies immediately
How to deploy your team based on their capabilities, not their role
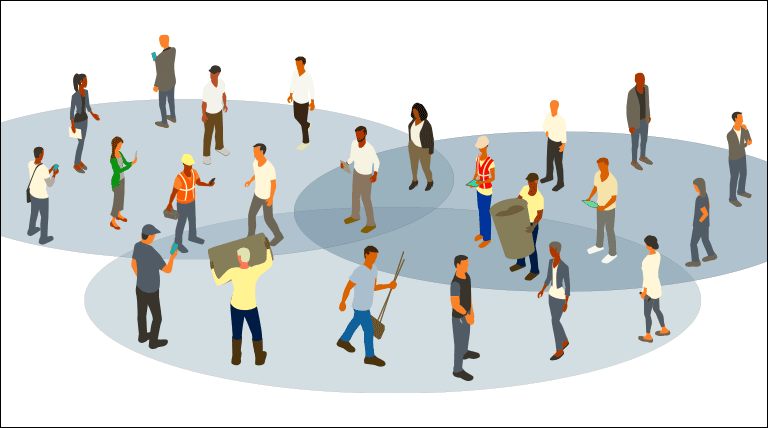
The gap between open positions and available frontline workers continues to choke operations across most industries. Organizations are getting creative at upskilling employees and automating their way through the pain. But an unexpected employee absence or resignation can cause ripple effects, if you’re not prepared.
A new strategy, deployed by an Acadia client, is worth considering. It takes advantage of expertise wherever it exists in the business, regardless of tenure or title, to ensure there are no staffing gaps in production.
To describe what they’re doing, I’ll start with an example of how a typical organization deploys resources.
Consider a manufacturing line that requires three employees to operate various pieces of equipment. All employees working the line must be proficient in Skills A & B.
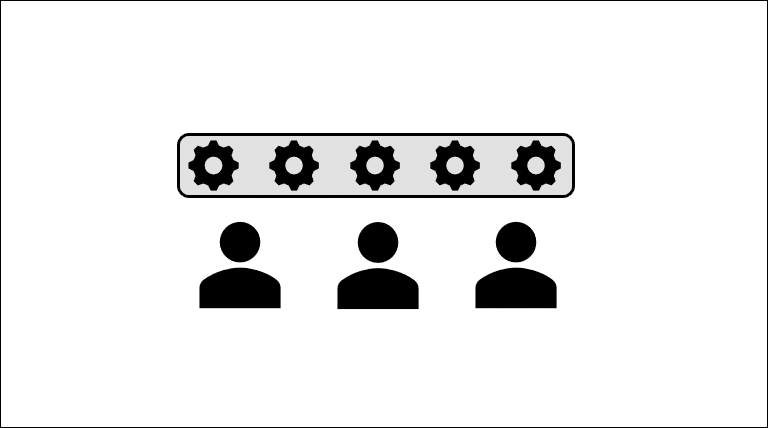
If one of the employees calls out sick, the shift supervisor will identify another available operator to fill in. The company may or may not have an up-to-date record of each employee’s capabilities. So, they’re choosing the replacement based on role and availability.
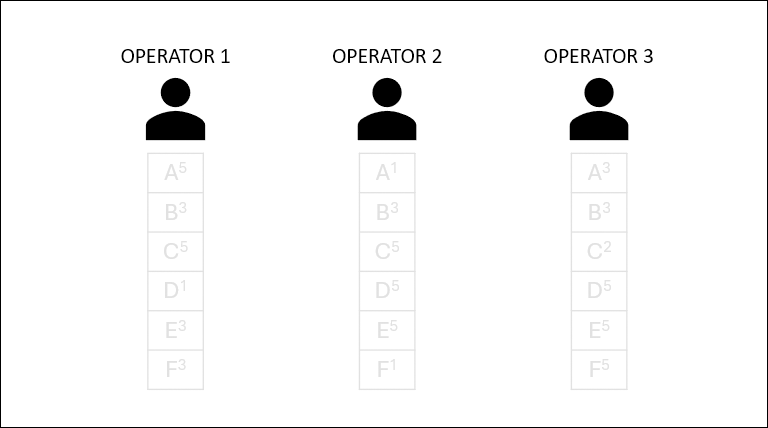
Promotions, department transfers, title and job role changes can obfuscate an operator’s underlying skills. Selecting a replacement by title or role alone means line performance could suffer based on the individual operator’s capabilities. In this instance, Technician 1 is the best option based on the skills they’ve acquired. The question is whether the shift supervisor has visibility into that skillset.
In the new paradigm, all employees’ skills are visible, regardless of their role. The shift supervisor can choose the most skilled employee for the job.
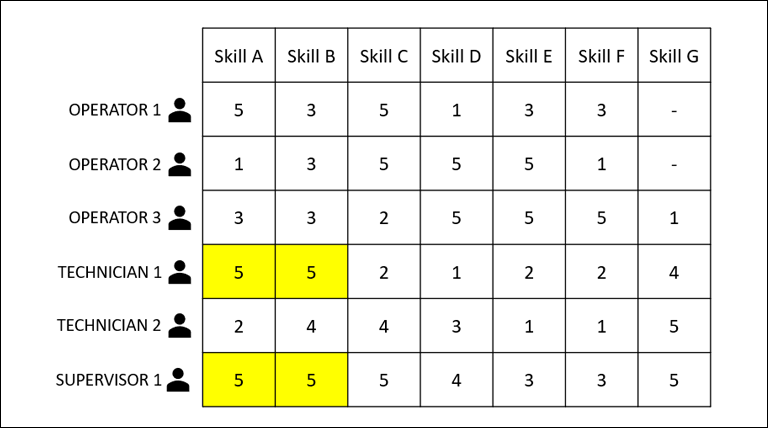
With this level of visibility, the absent operator can be replaced by another employee with the same level of competency. The line should perform just as well as if the operator hadn’t called out.
Our client has taken this concept a step further. They’ve broken down their shifts based on the employee capabilities required to maintain consistent production. Then, they schedule at least three people at the level of proficiency required for each skill. If someone calls out unexpectedly, at least two other people already on the shift are capable of filling in.
Plant managers use Acadia to build this redundancy by proactively developing employee skills. They use employee activity and training records to dynamically map each employees’ abilities to the facility’s needs. They identify soft spots and cross-train to fill the gaps.
This granular level of team skill visibility enables the company to get the most out of its existing workforce. Employees working in this environment are more engaged too. They have visibility into their progress, as they advance their careers.
We’ve worked with many clients to transition their existing employees and skill tracking spreadsheets into a dynamic model in Acadia. Depending on the size of the team it can be done in a matter of days or weeks.
Give us a call, we’d love to talk through your current set-up and show you how it could work in Acadia.
Ready to crush your goals?
"*" indicates required fields