How to change the tires while the car’s in motion
The Importance of Agility in Today’s Economic Environment
- Vast uncertainties make operating a business in today’s economic environment difficult – being able to respond quickly to unexpected events is critical.
- Common work practices have a failure rate ranging from 10 to 30 errors per hundred. When employees know where to turn for the answer, you can reduce human error, faster.
- Teams who can execute standard work consistently adapt better to changes in process and are inherently in a better position to respond when things go wrong.
- It takes longer to adopt process improvements if training is restricted to the classroom, or other resources provided away from where work is done.
- Create work instructions for your most important procedures and contingencies for errors that happen frequently.
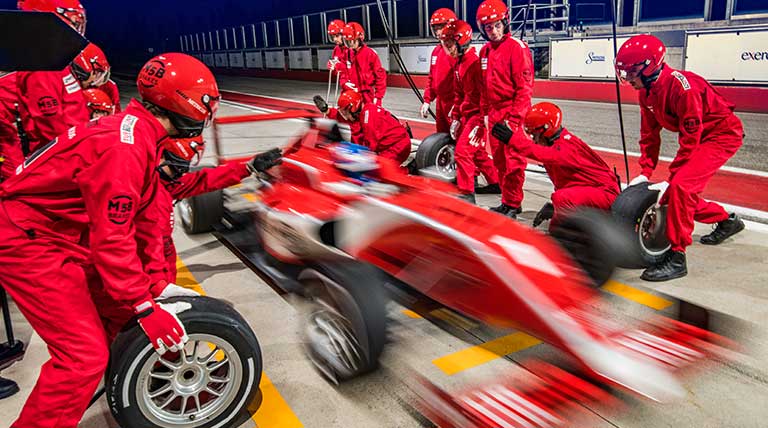
In less time than it takes to power on your phone, Red Bull Racing broke the pit stop record for the third time in one season. During Max Verstappen’s first stop of the Formula 1 Brazilian Grand Prix, his crew had him back on the track in an amazing 1.82 seconds,1 shaving six hundredths off their previous record. Not only did Verstappen finish first in that race, Red Bull set a new world record for tire changing that year and defended the DHL Fastest Pit Stop Award.
The Grand Prix, the most coveted championship in motorsports, began more than 70 years ago. Since then, racing crews have been continuously improving their capabilities. In the race’s first decade, a car’s pit stop time lasted about 67 seconds. A time that has been reduced to a mere 2-2.5 seconds2 on average today.
Time is everything in Formula One. And just as important as those who stand on the podium are the heroes in the driver’s pit crew. One to three times per race, a team of 20 people must perform 36 tasks in perfect synchronization. Their ability to respond quickly can make or break a race.
Each member of the pit crew has a specific set of tasks and only several tenths of a second to complete them. Tasks range from replacing tires to fixing mechanical problems. There are mechanics responsible for wing adjustments, stabilizing the car, and one for cleaning the driver’s visor.3
There isn’t time to see that everyone’s carried out their tasks. As a team, they need complete confidence that each crew member has completed their tasks correctly and is out of the way. This is where training comes in.
The training goal for each team member is to improve their performance through constant repetition. The team logs hundreds of hours of training each year following set protocols. And years of technological and mechanical development have allowed these crews to account for every possible contingency. After seventy years pit stop times have decreased nearly 96%!
You, obviously, won’t have the luxury of hundreds of hours of training for each of your team members. But you can give them the resources they need to execute quickly and accurately on every critical procedure. You can also help them be more agile when the unexpected comes up – even if they haven’t been trained on it before.
Execute with precision
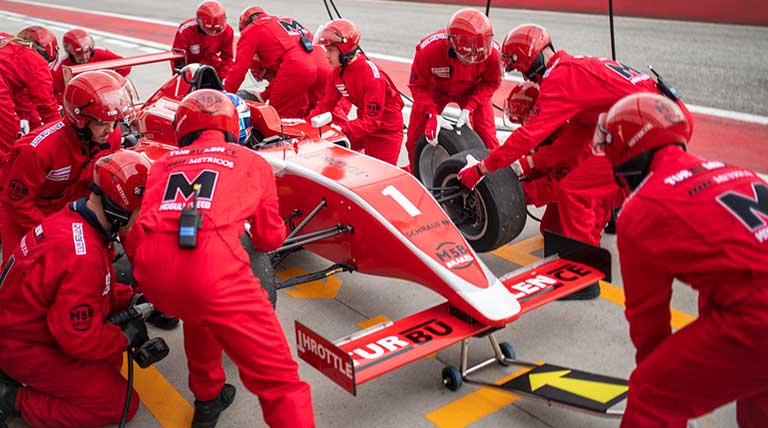
Just as F1 pit crews have evolved to execute their tasks with more precision and in increasingly shorter amounts of time, so have top performing businesses.
The most efficient and productive companies have evolved to help their teams move faster and eliminate errors. They’ve incorporated lean practices, streamlined procedures, and adopted tools to make their teams more autonomous.
It’s not enough to improve work instructions if they continue to sit in binders that nobody uses. It takes longer to adopt process improvements if training is restricted to the classroom. And it’s tough to deploy limited resources if you don’t know who can do the work and who can’t.
When you replace paperwork instructions with digital and make relevant information available to front line teams, you can expect a higher level of precision. Teams who can execute standard work consistently are inherently in a better position to respond when things go wrong.
Count on the unexpected
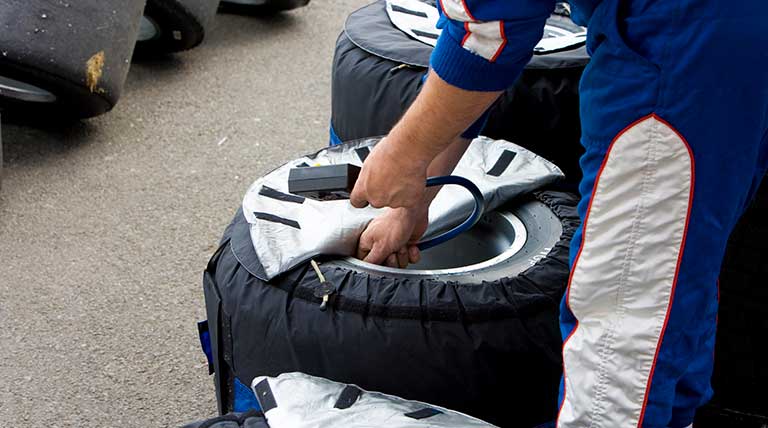
There are many uncertainties that make operating a business in today’s economic environment difficult: The ripple effect of supply chain issues that started in the pandemic. Unexpected and devastating weather and political events. Inflation, rising interest rates, and the possibility of a recession. None of these are knowable or controllable.
In the manufacturing industry, it’s estimated that one hour of downtime can mean as much as $6.45 million in losses,4 making something as simple as a power outage extremely costly.
What about human error? A misplaced comma or an extra zero on a contract. Training an employee and leaving out an important step. Misreading a document with poor resolution. These mistakes can add up quickly.
Fortunately, there are tools that can help your workforce be prepared to respond.
Prepare your team to respond
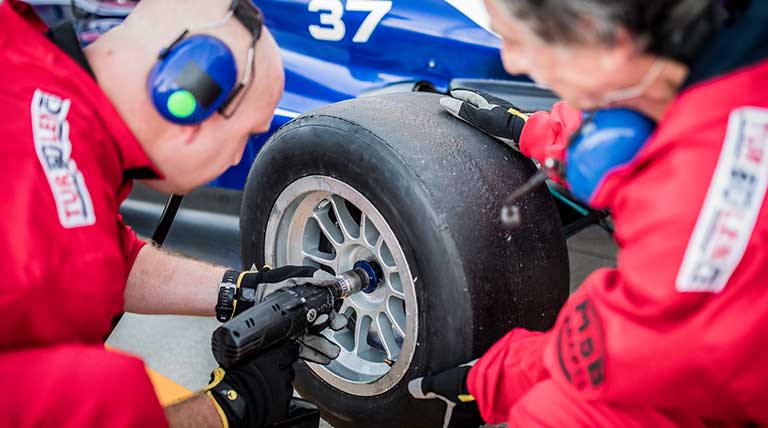
A reaction plan or troubleshooting guide can help you and your team minimize damage when the unexpected inevitably happens. Thinking through the steps to take when a problem occurs and making them easily available to your team can save tremendous time and resources.
It’s one thing to have a reaction plan. But if they’re hidden on a shared drive that nobody knows about, or in the head of your maintenance team, the response will likely take too long.
Instead, make your reaction plans available alongside your digital work instructions. That way, they’ll be accessible to everyone who needs them. For commonly occurring issues, use a QR code at the point of use to access the tasks and reduce the response time even further.
The typical failure rate in businesses using common work practices range from 10 to 30 errors per hundred activities5. Whatever can be done to simplify a response will reduce human errors.
Make agility possible
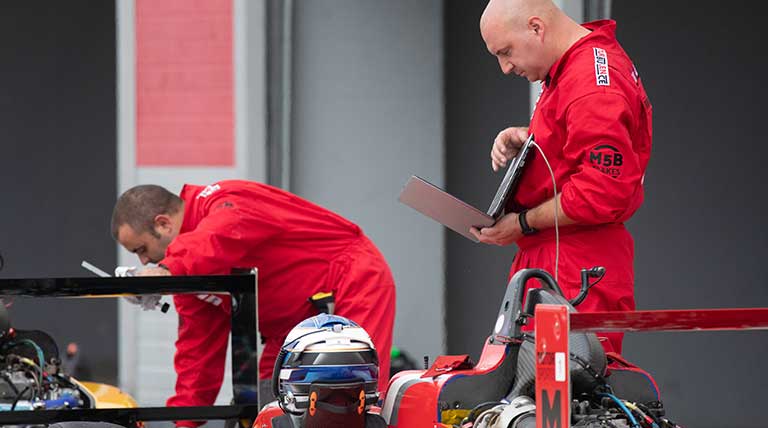
Our clients consistently describe dramatic improvements in agility after adopting Acadia. They can respond faster to any situation because every employee knows where to turn for the answer.
For example, early in the pandemic, a manufacturing client converted one of their production lines to make hand sanitizer. When manufacturing was losing 1.33 million jobs,6 our client was able to improvise and adapt.
By updating their SOPs in Acadia with the new product procedure, their team ran the same line just as efficiently.
Another client, an auto parts distributor, got stuck when one of their picking robots failed. The engineer who installed the machine had recently moved to another location. But before he left, he provided a trouble-shooting guide in Acadia. This enabled the contributors on the floor to quickly find an answer to their problem – saving hours of downtime.
It’s not just managers and leaders who can help make the team more agile. When an operator at a CPG client tried to use the new dock door in her facility, she found it unintuitive. After reviewing the manual, she quickly created work instructions in Acadia so the rest of her team didn’t have to. Spending an hour of her time, she saved tens of hours of training and confusion for everyone else.
Start small, start today
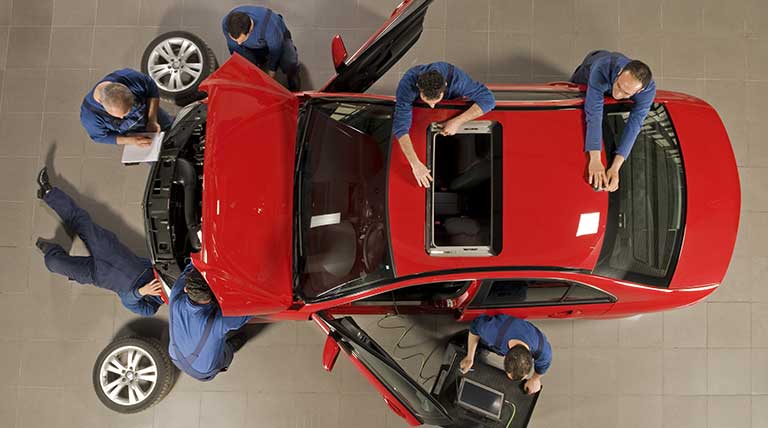
When the unexpected happens, don’t lose time and effort chasing around, trying to determine what to do. Provide a single source of truth where your team can go for the answer.
The advice we give our clients is to start small. Create work instructions for your most important procedures and contingencies for errors that happen frequently. Then expand your knowledge base over time to cover more of the business.
The important thing is to start today so you won’t be caught unprepared when the unexpected happens tomorrow.
Sources:
- New Formula 1 Pit Stop World Record (1.82s / Red Bull Racing / 2019 Brazilian GP)
- 1.82 Seconds To Change 4 Tyres Of A Formula 1 Car
- How to get your team to work like a Formula One pit crew
- What happens when manufacturing facilities lose power?
- How Much Do [sic] Human Error Cost Us Business?
- Manufacturing Loses 1.33 Million Jobs in April Because of COVID-19
Ready to crush your goals?
"*" indicates required fields